Introduction to Cartridge Heaters
Cartridge heaters are essential components in many industrial heating systems, known for their ability to provide precise and localized heat in a variety of applications. These versatile heaters are commonly used in industries such as plastics, packaging, food processing, aerospace, and medical device manufacturing. Understanding the materials and performance characteristics of cartridge heaters is crucial for selecting the right product for your specific application.
In this article, we will explore the different materials used in the manufacturing of cartridge heaters, their respective benefits and limitations, and how these materials impact the heater’s performance. We will also touch on the factors to consider when choosing the right cartridge heater material based on operational needs.
1. What are Cartridge Heaters?
Before diving into material comparisons, it’s important to understand what cartridge heaters are and how they work. Cartridge heaters are tubular heating elements that are inserted into a drilled hole or other form of mounting. These heaters are typically made from high-resistance wire, which is wound into a coil and then insulated and encased in a metal sheath.
The primary function of a cartridge heater is to generate heat through electrical resistance. This heat is then transferred to the object in direct contact with the heater. The design and materials used in cartridge heaters influence their efficiency, lifespan, and heat distribution.
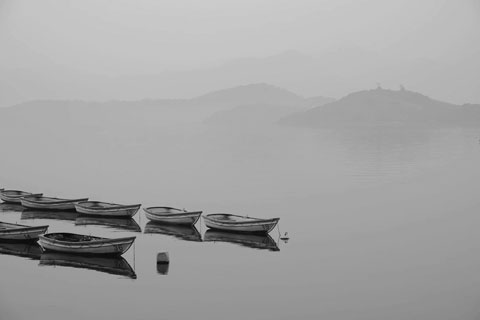
Heading One
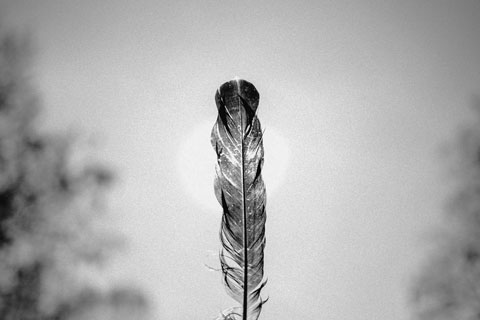
Heading Two
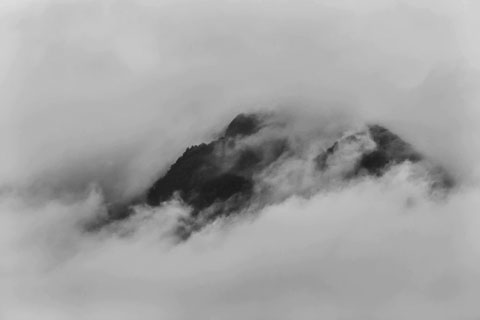
Heading Three
2. Materials Used in Cartridge Heaters
The material used for the sheath and internal components of a cartridge heater significantly impacts its performance. The most commonly used materials for cartridge heaters include:
Stainless Steel
Titanium
Incoloy
Copper
Aluminum
Nickel
Ceramic
Let’s look at these materials in more detail and explore their properties and applications.
3. Stainless Steel in Cartridge Heaters
Overview
Stainless steel is one of the most commonly used materials for the sheath of cartridge heaters. Known for its corrosion resistance, durability, and versatility, stainless steel is ideal for applications in which the heater will be exposed to harsh environmental conditions or require extended operational life.
Benefits
Corrosion Resistance: Stainless steel can resist corrosion from water, chemicals, and oils, making it perfect for use in food processing, plastics, and other environments where the heater may be exposed to aggressive substances.
Durability: It has excellent resistance to wear and tear, which extends the lifespan of the heater.
High Temperature Tolerance: Stainless steel can withstand high operating temperatures, typically ranging from 500°F to 1200°F (260°C to 649°C), depending on the grade used.
Cost-Effective: Stainless steel is relatively affordable compared to other high-performance materials.
Limitations
Lower Heat Conductivity: Compared to other materials, stainless steel is not the best conductor of heat, which may result in slower heat transfer in certain applications.
Limited Strength in Extreme Conditions: While stainless steel is durable, it can begin to lose strength in extremely high-temperature environments above its maximum tolerance.
Applications
Stainless steel cartridge heaters are widely used in applications like:
Industrial molding
Plastics extrusion
Food processing
Packaging machinery
4. Titanium in Cartridge Heaters
Overview
Titanium is often used in specialized cartridge heaters due to its outstanding strength-to-weight ratio and exceptional resistance to corrosion. Titanium heaters are particularly useful in industries that require both high heat transfer and resilience under extreme conditions.
Benefits
Superior Corrosion Resistance: Titanium has a higher resistance to corrosion than stainless steel, making it ideal for use in aggressive environments like those found in chemical processing, marine, and medical applications.
High Strength and Durability: Titanium maintains its structural integrity even under extreme temperatures and pressure, making it perfect for high-stress applications.
Lightweight: Titanium is much lighter than stainless steel, which can be advantageous in applications where weight is a concern.
Limitations
Cost: Titanium is significantly more expensive than stainless steel, which may make it less practical for some cost-sensitive projects.
Machinability: Titanium is harder to machine than stainless steel, making it more challenging and costly to manufacture cartridge heaters made from this material.
Applications
Titanium cartridge heaters are ideal for:
Aerospace and aviation
Marine environments
Medical device manufacturing
High-end food processing
5. Incoloy in Cartridge Heaters
Overview
Incoloy is a family of iron-based alloys that include high levels of nickel and chromium. These alloys are designed for high-temperature and high-corrosion environments, making them a go-to material in many heavy-duty heating applications.
Benefits
Extreme Temperature Resistance: Incoloy alloys can withstand temperatures well above 1000°F (538°C), making them suitable for applications with high heat exposure.
Excellent Corrosion Resistance: Incoloy is highly resistant to oxidation and corrosion, even in environments with extreme conditions such as acidic or alkaline environments.
Durability: Incoloy heaters are designed to perform well for long periods in extreme conditions.
Limitations
High Cost: Incoloy is a premium material, and the price can be prohibitive for low-budget projects.
Less Effective Heat Transfer: While it’s durable, Incoloy’s heat conductivity is lower than that of copper or aluminum.
Applications
Incoloy cartridge heaters are often used in:
High-temperature industrial processes
Heat treatment
Chemical processing
Furnace and oven heating
6. Copper in Cartridge Heaters
Overview
Copper is one of the best heat conductors available, which makes it an excellent choice for specific applications where efficient heat transfer is crucial. It is typically used in the internal components of cartridge heaters, such as the heating wire.
Benefits
Excellent Heat Conductivity: Copper’s superior thermal conductivity allows for faster and more efficient heat transfer, leading to quicker heating times.
Cost-Effective: Copper is less expensive than materials like titanium and Incoloy, making it an affordable option for many applications.
Ductility and Flexibility: Copper can be easily shaped and molded, making it ideal for manufacturing precise, custom heating elements.
Limitations
Corrosion: Copper is susceptible to oxidation and corrosion when exposed to harsh chemicals or moisture, which can reduce the lifespan of the heater.
Lower Strength: Copper is not as strong as other materials like stainless steel or Incoloy, which limits its use in high-stress environments.
Applications
Copper is commonly used in applications such as:
Rapid heating in small-scale applications
Precision instruments
Laboratory equipment
7. Aluminum in Cartridge Heaters
Overview
Aluminum is another material commonly used in the construction of cartridge heaters, particularly for the housing or sheath of the heating element. Its lightweight nature and excellent heat transfer properties make it an appealing choice for certain industries.
Benefits
Lightweight: Aluminum is lighter than many other metals, making it suitable for applications where reducing weight is important.
Good Heat Transfer: Aluminum’s thermal conductivity is quite high, making it ideal for applications that require efficient heat dissipation.
Corrosion Resistance: Aluminum naturally forms an oxide layer that protects it from corrosion, although it is not as resistant as stainless steel or titanium.
Limitations
Lower Temperature Tolerance: Aluminum may not withstand as high temperatures as other materials like stainless steel, making it less suitable for extreme heat applications.
Softness: Aluminum is softer than other metals, so it is more prone to physical damage and wear over time.
Applications
Aluminum cartridge heaters are often used in:
Heating systems with moderate temperature requirements
Lightweight applications
Electronics and semiconductor industries
8. Comparing Performance: Key Considerations
When choosing a cartridge heater material, several factors should be considered:
Temperature Range: Select a material that can handle the maximum temperatures required by your process.
Corrosion Resistance: Consider whether the material will be exposed to corrosive elements, which can shorten the heater’s lifespan.
Heat Transfer Efficiency: Choose a material that allows for efficient heat transfer, particularly in applications where precise heating is critical.
Durability: Consider the long-term durability of the material in the specific environment.
Cost: Factor in your budget, as high-performance materials like titanium and Incoloy can be expensive.
Conclusion
Understanding the materials and performance characteristics of cartridge heaters is essential to selecting the right heater for your application. Stainless steel, titanium, Incoloy, copper, and aluminum all offer unique benefits and drawbacks, depending on factors like temperature, corrosion resistance, and heat conductivity. By considering these factors carefully, you can ensure that you choose the right material for your heating needs.
At [Your Company Name], we offer a wide range of cartridge heaters tailored to various industrial applications. Our products are built with the highest-quality materials to provide optimal performance and durability. Contact us today to discuss your specific requirements and find the perfect cartridge heater for your business.
This article provides a thorough comparison of the materials used in cartridge heaters, ideal for both general readers and industry professionals looking to make informed decisions.